Introducing BotQ
Introducing BotQ, Figure’s new high-volume manufacturing facility for humanoid robots. BotQ’s first generation manufacturing line will be capable of manufacturing up to 12,000 humanoids per year. This is just the start and we will be scaling up considerably from here. Over the past eight months, the Figure hardware and manufacturing engineering teams have been building an efficient and scalable manufacturing process from the ground up, and we’re excited to share our progress to date.
Vertically Integrated Manufacturing: Figure has made the decision to bring the manufacturing of our humanoid robots in-house to control the build process, quality, and guarantee that we will deliver a high-functioning robot to market.
Building Software Infrastructure: For the last six months, we’ve been building the underlying software infrastructure that can support volume manufacturing (MES, PLM, ERP, WMS).
Robots Building Robots: Figure’s humanoid robots will be used in our manufacturing process to build other humanoid robots. This will take place this year. We project that the number of our humanoid robots involved will grow substantially over time to increase line automation.
Our Roadmap To Scalable Manufacturing
Rethinking the robot architecture
Achieving high production rate starts at the early stage of engineering design. After building and internally manufacturing Figure 02, the team recorded and analyzed cycle times for every process, from part fabrication to final assembly. The largest driver of assembly time started at the root: part count and manufacturing processes. Figure 02 was designed as a prototype and extensively used high complexity, tight tolerance, slow computer numerical control (CNC) machining processes. While CNC from billet is a great process for prototyping and holds value for high tolerance components, it does not scale well when trying to drastically reduce both part costs and time to make components. Part count was also heavily considered - if you have to join two parts, it takes time to perform that operation. Instead, if you can combine many parts into one, the cycle time goes down.
We have since completed the design of our next-generation robot, Figure 03, which is our production robot built for affordability and high-volume manufacturing. In order to achieve production manufacturing rates, we switched to tooled processes such as injection molding, diecasting, metal injection molding and stamping which enabled us to save thousands of hours on manufacturing. Parts that previously spent over a week on a CNC machine can now be manufactured in under 20 seconds with complex steel molds. Switching to these processes comes with a high capital cost, but the upfront investment is made back quickly when considering our robot volumes for 2025 and beyond. Rethinking the robot architecture also led us to stand up two new teams - a safety team and a reliability team.
In addition to manufacturing at high rates, we are also ramping up our focus on robot reliability. The reliability team, located at BotQ, is in charge of running highly accelerated lifecycle tests to help us understand the lifespan of the robot. The reliability team needs specialized equipment, including high temperature ovens, dedicated actuator testers, and failure analysis equipment to understand root cause failures. Using this data, we can inform the robot designers of improvements needed to ensure our reliability metrics are met.
Building the supply chain
Humanoid robots, unlike most other industries, do not have well established supply chains with various tiers of manufacturers building modules of the system. This has ultimately led us to design almost the entire robot from scratch including the actuators, motors, sensors, battery pack, and electronics. The lack of a mature supply chain has been one of the biggest hurdles our team has faced when defining how parts would be made and where. What would we vertically integrate, what would we choose to tackle in house? We made the decision to focus heavily on the assembly of our core technology in-house (actuators, hands, batteries, final assembly) and when needed, leverage outside vendors for piece part manufacturing. In addition, we hired a team of world-class global supply managers to help form strong partnerships with vendors who have the expertise to produce our complex components. Our robot has over 3 dozen unique commodities, many of which require unique processes such as motor winding, flexible OLED screens, or precise optical designs. All of our external partners were selected to be able to scale with us: our supply chain can easily scale to 100,000 robots or 3,000,000 actuators in the next four years.
Building the manufacturing team
The next organization that we needed to develop was the manufacturing team. Over the last six months, we’ve hired experts who spent their careers designing lines, optimizing those lines and understanding how to optimize the process of turning materials into products in an efficient and rapid manner. Our manufacturing engineers are responsible for breaking the robot assembly up into sub-stations, selecting the proper tools to join the parts together, designing and procuring fixtures for the assembly line, and understanding how to test the parts as they rapidly turn into a robot. In addition, the engineers provide design change feedback to our mechanical, electrical, and software teams to decrease production cycle time.
One key aspect of new product manufacturing is understanding which operations on the production line should be automated and which should be manual. Historically, humanoid robots have been built in low volumes and automation has been rare. Figure has chosen key elements of the process to automate in the short term by looking at metrics such as quality and speed. An example of automation for quality is the automated grease dispense station for our motor gearboxes: we can control the location and volume of the gearbox grease far more accurately with an automated dispensing tool than with a manual grease gun. An example of automation for speed is our cell test and load station: a robot is far faster than a human at picking up, scanning, and testing every battery cell before assembly into the battery pack.
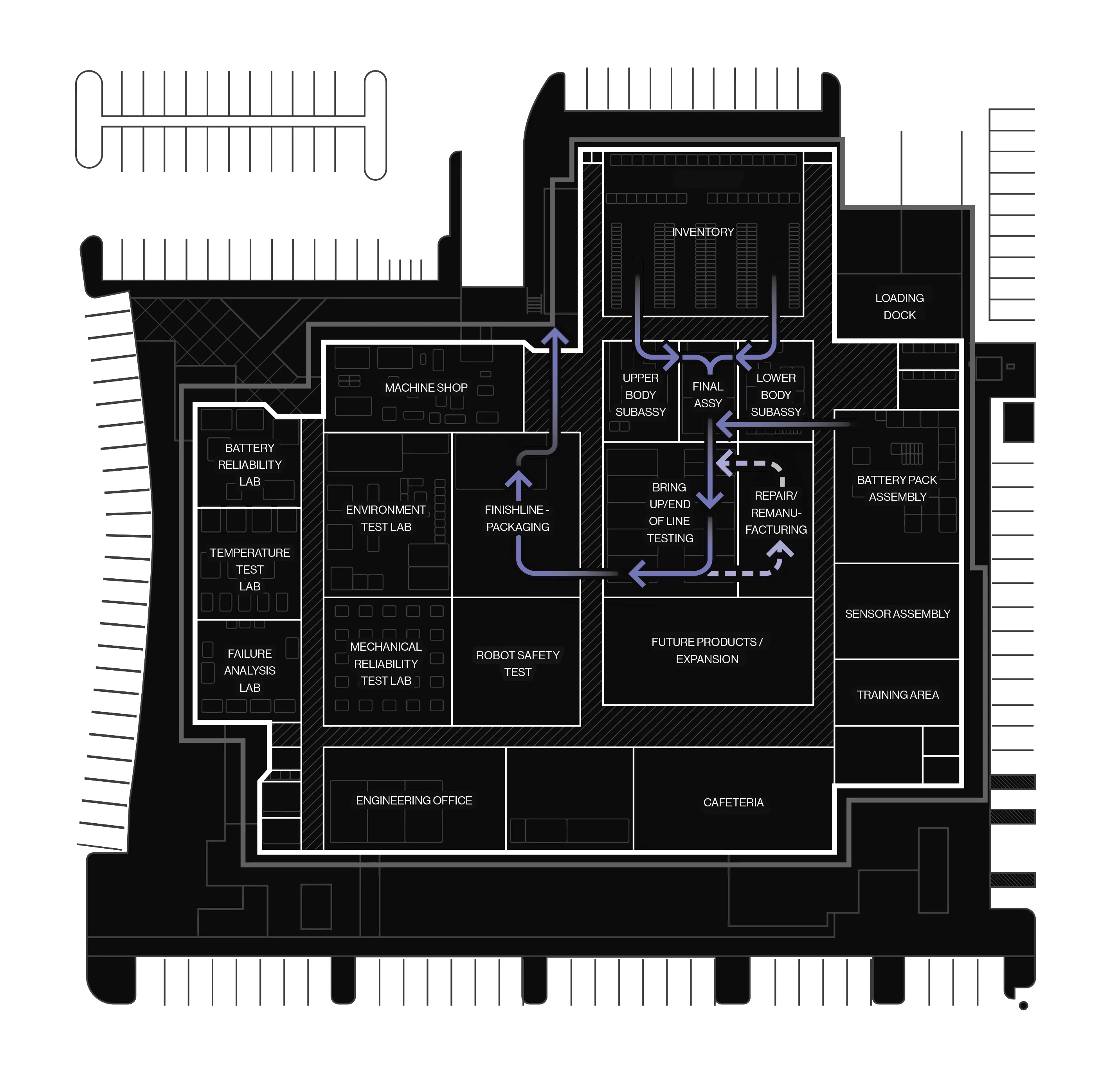
Standing up the infrastructure
Manufacturing comes with an enormous amount of infrastructure needed to make the process flow smoothly. In order to stand up a successful factory, we added new tools to our development process - namely Product Lifecycle Management (PLM), Enterprise Resource Planning (ERP), Warehouse Management Systems (WMS), and most critically - a custom built Manufacturing Execution Software (MES).
Manufacturing Execution Software (MES) - This is the backbone of our manufacturing operation and is being built in-house. MES integrates all aspects of production into a single, real-time digital ecosystem. From tracking parts through the supply chain to monitoring assembly efficiency and ensuring stringent quality control, MES allows us to operate at peak efficiency. Our MES system integrates with our IOT devices to monitor process flow, track genealogy and provide a digital database of all the test data related to every component in the robot.
Robots building robots
As a key innovation, BotQ integrates Figure humanoid robot automation into our own assembly lines. With the introduction of our internal AI, Helix, we will be capable of using the robot to assemble key components of our production line and act as a material handler moving goods between different stations without needing to install bulky and inflexible conveyor systems. The combination of AI-driven automation and human oversight allows for a hybrid workforce that maximizes speed, precision, and adaptability. By employing robots to build more robots, we can accelerate production timelines while minimizing human intervention in repetitive tasks, ultimately setting the foundation for the future of autonomous manufacturing.
Conclusion
We have presented BotQ, a high-volume manufacturing facility with initial production lines capable of manufacturing up to 12,000 humanoids per year. Our robot volumes will only grow substantially from here. We have outlined the plan stating our full robot architecture redesign which includes integrating supply chain and introducing new enterprise software for scalability. BotQ represents a major leap in humanoid robot manufacturing.
If you’re interested in supporting the design, manufacturing, or production teams at Figure, click here and apply.